Plastic Mouldings stands as one of the most pivotal processes in modern manufacturing, shaping the everyday objects that populate our world. From intricate medical devices to durable automotive components, plastic moulding offers immense versatility. Each moulding method caters to distinct use cases, offering manufacturers flexibility in material selection, design intricacies, and production scale. Understanding these different moulding types is crucial, not only for engineers and product developers but also for industries striving for efficiency and innovation.
Knowing the nuances between the various plastic moulding processes enables businesses to make informed decisions that directly affect product quality, cost, and production speed. As industries continue to evolve, the importance of selecting the appropriate moulding method becomes increasingly essential.
Plastic Moulding Processes
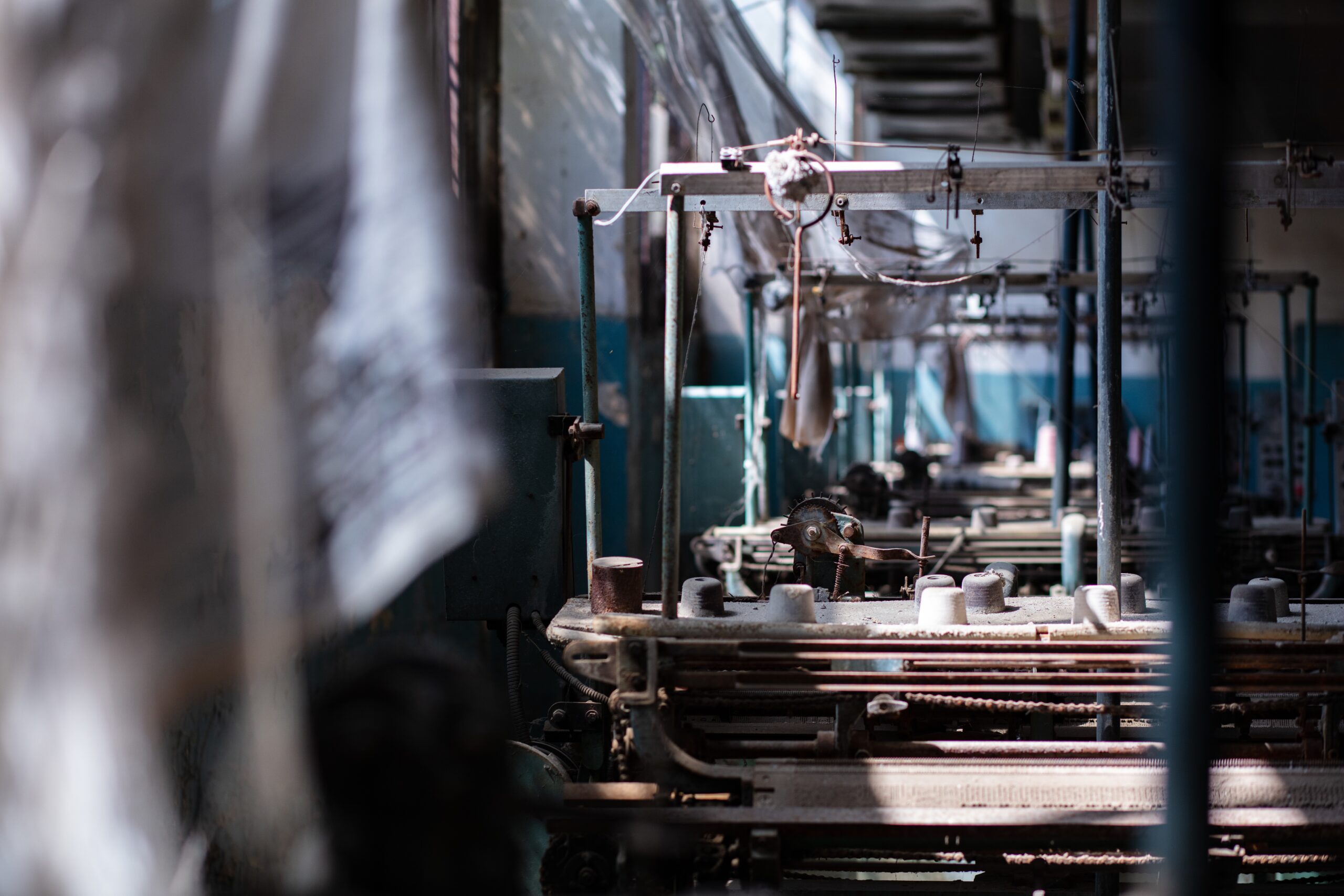
Plastic moulding, in its simplest form, involves shaping plastic materials into specific forms by using a mould. This technique allows for mass production of items with precision and uniformity, reducing costs and ensuring consistency in product design. Moulding processes are employed across numerous sectors, each offering distinct advantages and limitations depending on the application.
Typically, the primary materials used in plastic moulding include thermoplastics and thermosetting polymers. Thermoplastics, such as polyethylene and polypropylene, soften when heated and harden upon cooling, making them highly versatile. Thermosetting polymers, on the other hand, solidify irreversibly when heated, offering greater durability for certain applications. Selecting the right material and process is paramount to ensuring optimal product performance.
1. Injection Moulding:
The Most Versatile Process
Injection moulding is arguably the most widely used plastic moulding process due to its unparalleled versatility. The process begins with the melting of plastic granules, which are then injected into a mould under high pressure. Once cooled, the plastic solidifies, forming the desired shape.
This method is well-suited for creating a vast array of products, ranging from small components such as smartphone cases to larger items like automotive dashboards. Its ability to produce complex shapes with high precision, coupled with the capacity for mass production, makes injection moulding indispensable to numerous industries. The automotive, consumer goods, and medical sectors are some of the key beneficiaries of this process, relying on injection moulding for both everyday products and highly specialized components.
2. Blow Moulding:
Best for Hollow Shapes
Blow moulding offers a unique approach to producing hollow objects. The process involves inflating heated plastic within a mould to form a cavity. Once the plastic expands and cools, it hardens into the desired hollow shape.
Common products created through blow moulding include bottles, containers, and fuel tanks. Its ability to form hollow parts efficiently makes it a preferred method in industries like packaging and automotive manufacturing. Packaging companies use blow moulding to mass-produce lightweight, durable bottles for beverages, while automotive manufacturers rely on it for crafting complex fuel tanks and air ducts.
3. Rotational Moulding:
Ideal for Large, Durable Items
Rotational moulding, often referred to as rotomoulding, excels in creating large, seamless products with superior durability. This process involves heating plastic within a rotating mould, ensuring that the material coats the entire interior evenly. The mould is slowly cooled, producing a hollow, uniform structure.
One of the significant advantages of rotational moulding is its ability to create products with robust walls and minimal weak points, making it ideal for large items such as water tanks, outdoor furniture, and playground equipment. Its relatively low tooling costs also make it attractive for low-volume production of large objects that require high durability.
4. Compression Moulding:
Cost-effective for Complex Parts
Compression moulding involves placing a preheated plastic material into an open mould, which is then compressed to form the desired shape. The mould remains under pressure until the material cures, solidifying into the final part.
This process is particularly advantageous for manufacturing large, complex parts with intricate details. Items such as electrical switchgear, automotive parts, and high-strength structural components are often produced using compression moulding. Industries that prioritize cost-effectiveness for complex parts, such as aerospace and electronics, heavily rely on this technique for high-strength, detailed components without excessive material waste.
5. Thermoforming:
Quick and Efficient for Thin Plastic Sheets
Thermoforming is distinct from other moulding methods, as it primarily uses thin plastic sheets that are heated until pliable. The sheet is then formed over a mould using vacuum pressure or mechanical force, after which it cools and solidifies.
This method is quick and efficient, making it an excellent choice for applications requiring lightweight yet sturdy products. Thermoformed products are ubiquitous in the food packaging industry, where items like disposable containers and lids are mass-produced. Additionally, thermoforming is often used for creating custom trays and covers in the medical field, where fast production times and hygienic materials are paramount.
6. Extrusion Moulding:
Continuous Production for Long Products
Extrusion moulding is designed for the continuous production of long products. In this process, molten plastic is forced through a die, forming long, uniform shapes. Once extruded, the material is cooled and cut to the desired length.
This method is well-suited for products such as pipes, tubing, and window frames. Its ability to produce continuous lengths of material with consistent cross-sections makes it indispensable in construction and manufacturing. The extrusion process is both efficient and cost-effective, allowing for large-scale production without compromising quality.
7. Vacuum Moulding:
Simplified Production for Prototyping
Vacuum moulding, a subset of thermoforming, simplifies production, particularly for prototyping and small batch manufacturing. This method involves heating a plastic sheet and drawing it over a mould using vacuum pressure, resulting in a detailed form.
Its simplicity and cost-effectiveness make vacuum moulding an attractive option for low-volume production runs, where the focus is on speed and flexibility rather than mass production. Prototyping, custom packaging, and product design testing are common use cases, allowing manufacturers to iterate quickly and efficiently.
Comparison of Plastic Moulding Methods
While all moulding techniques share the goal of shaping plastic into functional products, each method offers unique advantages and limitations. Injection moulding excels in mass production, while blow moulding is optimal for hollow shapes. Rotational moulding provides unmatched durability for large items, whereas thermoforming and vacuum moulding are efficient for thin, lightweight applications.
Several factors influence the choice of moulding process, including the material, product design, production volume, and cost constraints. Understanding these variables allows manufacturers to select the most appropriate moulding technique for their specific needs, balancing precision, efficiency, and cost-effectiveness.
Conclusion
Plastic moulding processes play a critical role in modern manufacturing, enabling the creation of a diverse range of products. From the versatility of injection moulding to the durability of rotational moulding, each method serves specific industries with tailored solutions. Choosing the right moulding technique ensures that products meet quality standards while remaining cost-efficient, supporting innovation across sectors like automotive, packaging, and medical devices.
By understanding the different moulding techniques and their respective use cases, manufacturers can make informed decisions that optimize production processes and deliver products that meet market demands.
Please find out new blogs at devomech solutions.